Behind the testing error is found in the data is read, check out as a result, their own welding RS485 lines there is a problem,
Must be welding below, 35 sub, 46 nipple,
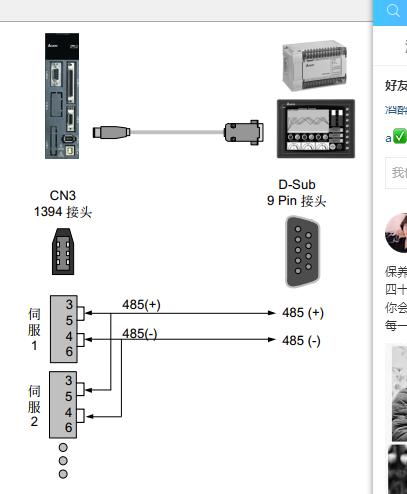
1. P3-00 set to 2//address is 2
P3-01 0033 baud rate 38400
P3-02 0011 communication protocol 1:7, E, 1 (MODBUS, ASCII)
P3-05 0000 standard MODBUS RS485 communication,
Set the data above, you can now preliminary writing PLC program,
2. P4 040-05 address ah (test)
Control mode: 1-5000 for inching speed
/4998: CCW direction inching
/4999: the CW direction inching operation
/0; Stop running,
By of servo drive P4-05, speaking, reading and writing can make servo motor to realize a simple test, 0 servo motor stop, send within 1-4997 Numbers is to set the speed of the servo motor, 4998 motor CCW, 4999 motor, the CW position 0 motor stops,
After testing the above data, you can now make servo read the current position,
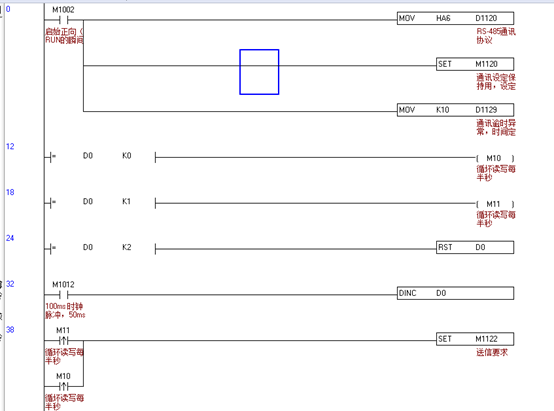

Simple explanation: H4 and H6 can be changed, such as D600 numerical is set up, let's read the inside of the P - 002 voltage, for example, servo specifications, reference should be set to 14, the main circuit voltage, then MODWR K2 H4 K14, servo drive panel the Numbers shown on the main circuit of voltage,
3. The key here, by 485, now let's make up to servo A2 moves up the parameters of the need to the following
Simple process is through the P5-07 parameter control servo motor, carried out in accordance with the PR mode movement way,
P0-02 set to 00, according to the number of pulses return
P1-01 is set to 1, to PR mode,
P6-00 origin definition set 0, for example, when to return to complete, stop, need to set to slow down time, see the manual, the specific set of origin P5-04, set the P5-04 to 108, the specific meaning is when you meet the limit direction reverse, returns to find Z phase, directly define the origin in so far as the origin,
P6-01 origin definition of value, the personal habits, my side is set to 0
P6-02 custom properties, such as I set to 1, compared to constant speed control, and then send 1 to 5 to 17, back to the pattern of P6-02 do constant speed control and running speed according to the parameters of the P6-03 inside
P6-03 according to P6 front - 02 is set to 1, the speed of the side is set to 2000, and then send 1 to 5 to 17, back to the pattern of P6-02 do constant speed control and speed according to the inside of the P6-03 2000 run
P6-04 custom properties, positioning control for 2,
P6 is set to 10000-05 (the final location of the servo operation point, the number of pulses on behalf of the servo feedback), suggests that if the P5-07 hair 2, then PR program is executed, the inside of the P6-04 and P6-05 program execution, do positioning servo motion, motion until 10000 to this place,
The parameters of the P6-06 to P7-27, similarly to the above Settings,
Set the data above, absolute position encoder options now,
P2-69 is set to 1, the purpose is, when the power is the location of the encoder will memory, again, when the power is the last time the location of the will recount, displayed in the panel,
P0-49 is set to 1, after the setting, will the current panel encoder numerical memory to P - 52, explain, in the offer is P0-50 to P0-52, such as the current panel on my side value is 800, so will write numerical P0 to 52,
P2-70 is set to 1, will read the numerical units set to pulse, popular point should be pulse number
P5-07 by written to 0, start of origin (P6-00 and P6-01 program),
//write 1-63, began to perform the specified PR program, equivalent to D1 + CTRG + POSN (by setting the inside of the P6-00 to P7-27 parameters can make the program according to the parameters to run)
Write 1000, STOP command, equivalent to DI: STOP
P5-07 by written to 0, start of origin (P6-00 and P6-01 program),
//write 1-63, began to perform the specified PR program, equivalent to D1 + CTRG + POSN (by setting the inside of the P6-00 to P7-27 parameters can make the program according to the parameters to run)
Write 1000, STOP command, equivalent to DI: STOP
P5-07 through written 1, begin to execute (P6-02 and P6-03 program), stop send the P5-07 1000 can directly,
P5-07 through writing 2, begin to execute (P6-04 and P6-05 program),
Constant speed control stop sending 1000. Positioning control can be set up, after location to stop and position to the execution of a function, after this you can refer to the manual application of ASDA - A2 series, other manual individuals is only a reference, the final reference manual from ASDA - A2 series,
Note:
1. After each update P0-49 data inside, must return to the origin, so as to execute, PR locator.
2. The orientation program is to return the data from the panel, such as you send 10000, servo will return to the 10000 position from the other position, and displayed on the panel, if you need other functions, please refer to the manual application in ASDA - A2 series,
3. This program can manually panel data to verify first, and then making PLC can,
4. Touch screen can also be used to control and personal advice in MODBUS RTU mode,